Feature
Label production 4.0
EU and US experts tell Liz Newmark how automated labelling production technology is moving the packaging industry forward.
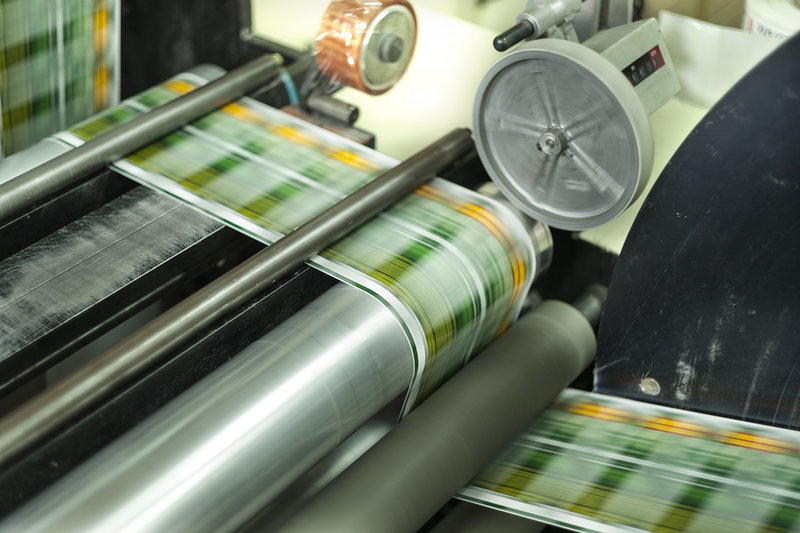
The packaging industry is being driven towards higher levels of automation. Credit: Shuttersock
Label-making automation is increasingly important to the global packaging industry. Indeed, US-based global identification and compliance solution specialists Brady Corporation calls automated labelling a “must-have” – saying that the question is not if a company will automate its labelling process, but when.
A report by US-based multinational consultants Smithers on the future of label printing identifies automation not just as a key technology trend but one that can significantly disrupt the label printing market.
New demands on label printers for shorter print runs, faster turnaround and greater flexibility are driving the industry towards higher levels of automation, said Smithers. Printers are investing in sophisticated management information systems, integrated with specialised inspection and colour performance software and technology and fully automated press and finishing line set-up systems.
Linking every stage of production
In the US, Rob Mayerson, president of Wisconsin-based Label Traxx, told Inside Packaging the full value chain has progressively become more automated, with the rate of change continuing to accelerate: “Digital processes are being introduced, and more importantly, linked together at every stage of production,” he said.
This phenomenon extends beyond digital print and finishing. We see all steps – from order to approvals to production to invoice, shipping and collection being automated and informed by other digital steps in the process.
In addition, the Label Traxx chief said automation helps label-making efficiency: “We see the time spent waiting for answers and delays caused by orders sitting in queues being reduced dramatically.”
Turning to financing and environmental concerns, Mayerson told Inside Packaging: “The biggest area of cost reduction and sustainability improvements are achieved through automated scheduling. Complexity of a typical label converter has progressed to the point that software and computers are best equipped to analyse the larger backlog of orders and associated details to most efficiently sequence orders to drive efficiency.”
Indeed, he said, this means that “within 30 days of transitioning to automated scheduling, one customer achieved a 20% decline in waste – benefiting the label converter and the environment”.
A move towards automation and its capacity to reduce human error, increase label production speed, and integrate label and document printing, is also being seen elsewhere in the world.
Companies, including Canada-based CCL Label, and European printed label manufacturer Stratus Packaging, say that innovation is important to keep up with changing standards and regulations to develop and manufacture safe and efficient products.
Reinhard Streit, vice president and managing director of CCL Label, which provides solutions to the home and personal care, premium food and beverage, healthcare, automotive and consumer markets, told Inside Packaging: “In recent years, the label and shrink sleeve sector has seen significant advances in the automation of production processes. Many production lines are equipped with automatic print control systems for colour management and label die-cutting precision.”
For Streit, head of CCL’s food and beverage division, precision significantly impacts the label application process on customers’ production lines. He said the high quality and reproducibility of the labels supplied are key elements influencing the efficiency of production lines in many processing sectors.
The benefits of automated label processes
In short, “the use of automated processes in label production has brought benefits such as reduced ‘make ready’ times, increased productivity and reduced production waste, allowing for more sustainable production.”
Streit said that to provide customers with high and reproducible quality in the printing process, hybrid devices are used that combine different printing technologies within a single printing machine.
“This combination of printing techniques is not simple and requires a high degree of expertise from both the machine manufacturer and production teams. In the case of hybrid machines, different printing techniques are combined (each requiring a different type of ink, printing plates, ink transfer and drying process) and precise control of the production process.”

Mines in Bayan Obo in Inner Mongolia, China, extract one the largest deposits of rare earth metals found in the world. Credit: Bert van Dijk/Getty images
This will result in “unique solutions in the appearance of the label,” he said. Most importantly, however, is that the labels will “apply well and flawlessly to the products to be decorated with them,” Streit noted.
Label automated success is not all about speed, although some machines on the market from global giant Brady Corporation and Belgium’s Weber Marking Systems, for example, have impressive results.
Brady’s BradyPrinter A5500 flag printer applicator prints and applies flags in as little as five seconds, while Brady’s Wraptor A6500 wrap printer applicator also takes only five seconds to print and apply self-laminating wrap labels. Weber’s Legi-Air 4050-B and Legi-Air 6000 label printer and dispensers reach speeds of up to 270 labels per minute and 2,400 labels per hour, respectively.
The correct choice of substrates and choice of adhesives is also important. “Sustainable labelling materials that support the recycling process by easily separating them from the packaging, or, in the case of returnable packaging, allowing the packaging to be reused easily, quickly, at low cost, and without trace are becoming increasingly important,” said CCL’s Streit.
Choosing the right materials and printing techniques
In short, while automation is very important to boost productivity and minimise errors, it is equally important to have “expert knowledge in selecting the right materials, printing techniques, and in understanding and developing application processes,” the CCL vice president added. “Combining good printing craftsmanship with modern solutions and openness to the latest technological developments at the present time guarantees success.”
Stratus Packaging CEO Isidore Leiser also emphasised the importance of sustainability with the company’s range of self-adhesive, booklet, dry peel coupons, sleeves and in-mould labels. For example, its BOBST M5 flexo press features the DigiFlexo system which makes print pressure pre-set and register adjustments fully automated: “This leads to reduced waste during set up, particularly with multi-colour jobs and consistent printing quality during production,” Leiser said in a January memorandum.
In future, Leiser will continue to seek innovations “that can make a real difference”. He said Stratus Packaging navigated 2022 successfully, “thanks to our high levels of automation and ability to manage our supply chain…”
In addition, he believes data management will grow in future and labels “are a good vehicle to manage various information and data”, while label converters need to be “ready for a new reality where machines will become more automated and intelligent”.