Feature
Cloud solutions for packaging supply chains
New developments in cloud technology are helping packaging manufacturers worldwide compete. Liz Newmark investigates.
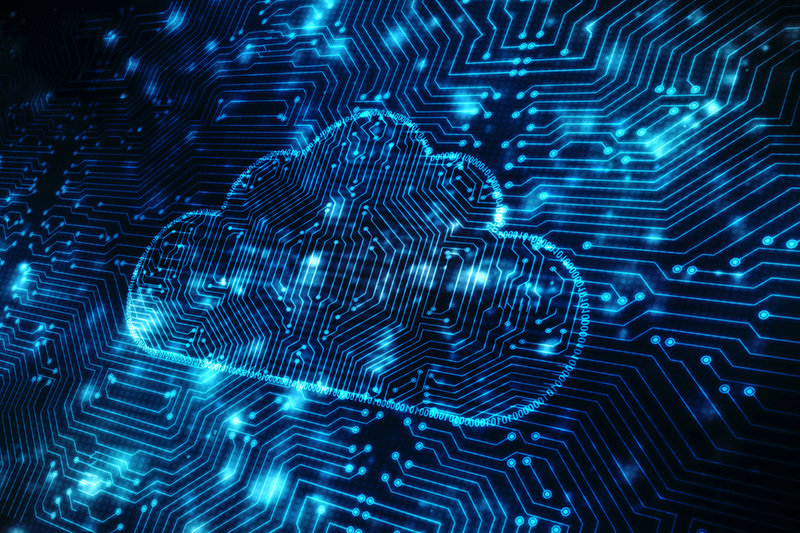
Credit: Shuttersctock
Digitisation is seen increasingly as an opportunity rather than a risk. Digital or cloud-based solutions range from simple printers to whole document and artwork editing systems. For example, Japanese auto-identification (ID) solutions business SATO Holding Corporation, headquartered in Japan, offers cloud-based printing solutions for packaging with sophisticated machines such as its label printer CL4/6NX-J.
“At the heart of our SATO business is tagging — attaching ‘things’ with data and feeding it into systems to put it to good use,” SATO CEO Hiroyuki Konuma said in a company briefing note. “Tagging technologies of today like RFID [radio frequency identification] handle more data and involve greater complexity compared to price tags and barcodes which emerged in the 1960s to 1980s.”
For the organisers at Interpack – a packaging industry trade fair being held on 4-10 May in Germany – digitisation is the focus of the supply chain. “Digitisation is cloud-based, and data analysis will reduce down times and increase production capacity at the same time,” said an explanatory note for industry participants.
This view is backed up by Germany-based digital technology experts, VN Reproduktion und Kommunikation GmbH: “Looking to increase productivity, minimise human error and reduce complaints, we embrace automation,” media technician and customer adviser, Jens Fechtel said.
With cloud technology - packaging and displays are developed online, size and material are precisely calculated and drawings are produced and transferred to physical substrates such as glass, sheet metal, paper or plastics using 3D tools, Fechtel explained in a note for Hamburg-based quality control company EyeC Inspection Systems: “Along with the highest possible level of user friendliness, new cloud-based tools help put an end to location-based work, so remote or hybrid work is possible.”
Multilingualism, the shorter time-to-market, frequently changing artwork and constantly changing regulations; as well as compliance with sensitive information, such as sales descriptions, allergens or nutritional values, present quality control challenges at pre-press stage.
To find and alleviate mistakes at this stage, VN has installed EyeC Proof Text automated web-based solution for text and artwork, as “an alternative to time-consuming and personnel-intensive manual checking processes”.
The text comparison and artwork proofreading system compares the customer’s proof with the final artwork. An intelligent algorithm finds and evaluates discrepancies between documents including text content and font.
This means that “operators have as little manual reworking to do as possible and the employees can concentrate on other things in the final inspection,” he said.
And as the software is offered as a ‘software as a service’ – SaaS application, “it integrates into the company workflow without much administrative effort,” as clients access software via the Internet instead of installing it themselves.
Indeed, Rob Mayerson, president of US-based Label Traxx, a leading MIS/ERP (management information system/enterprise resource planning) business for the labels and flexible packaging segments of the printing industry, told Inside Packaging that cloud technology is cost effective for packaging companies and services.
“Cloud technologies are enabling stakeholders to participate in the order management process from any location on any device,” he said. “Customers can place orders, check history and approve proofs with a tap from their mobile device at any time. This greatly improves convenience for the customer and efficiency for the packaging company.
“The ordering process is streamlined, while wait time is drastically removed for all parties,” Mayerson continued. “Similarly, sales executives on the road can conduct business and dramatically improve their efficiency by interacting with the MIS from their mobile device.”
Netherlands-based Cambrian Technologies, that specialises in cloud-based managed services, also says cloud-based innovations will help the packaging sector improve their products.
“Cloud solutions using machine learning continuously inspect production lines and can identify defects (visually),” Cambrian Technologies co-founder and director Dionysis Linardatos said. “This can help improve quality and lower production costs.”
In addition, with cloud technology, it is easier to improve packaging design workflows through automation, as well as on-demand computing capacity and workflow automation and orchestration, Linardatos told Inside Packaging.
Meanwhile, cloud technology supports sustainability in several ways, he added. This is because, “running information technology (IT) workloads in the cloud will have a substantially lower CO2 footprint than running the same workloads on premises.”
The cloud also offers various supply chain optimisation solutions to help packaging be produced and shipped to the customers (who place goods in the packages) in a sustainable manner.
In addition, “it is possible to build a digital twin of a factory and optimise its operations. This can be applied to manufacturing plants where packaging is produced,” the Cambrian chief added.
Technology giant ABB is one company using digital twin expertise. It uses cloud-based technology for simulation software that can help packaging companies pallet their goods with ABB robots.
“New web-based tools like RobotStudio Cloud bring a new level of agility and flexibility to manufacturers in how they plan and design their robotic automation solutions,” Marc Segura, president of ABB’s robotics division, told a December (2022) launch of this technology.
New features in RobotStudio Cloud include version control, allowing users to keep track of changes and have full transparency of any amendments, said ABB: “With complete knowledge of who edited the programme and when, developers can cut the time needed to resolve errors and performance issues.”
Why has the use of RFID fluctuated over the past decade?
“First has been the cost”, says Franck Germain, VP marketing at Linxens, a global technology company that manufactures electronic components for security and identification, including RFID antennas and inlays. “Twenty years ago, the cost of implementing RFID tags and the ecosystem (software) was much more expensive than today. Solutions were also much more complex to implement [then], whereas today there are a lot of companies in the market offering multiple solutions.”
He adds that in the early 2000s there were no set standards for RFID in the pharma industry, so the compatibility between systems was not guaranteed. There were also, and still are, some privacy concerns about what exactly is tracked and how data is used.
Twenty years ago, the cost of implementing RFID tags and the ecosystem (software) was much more expensive than today.
Franck Germain, VP marketing at Linxens
In recent times, various global administrators have issued regulatory standards. The US Food and Drug Administration (FDA) has provided guidance for the use of RFID in the drug supply chain and to standardise the data format. In the US Drug Quality and Security Act (DSCSA), the FDA mandates that manufacturers and trading partners should have full interoperable electronic track and trace systems in place by November 2023. The European Medicines Agency (EMA) has produced similar recommendations, but with a focus on using RFID tags to track the movement of drugs through the supply chain, and instructed companies to implement appropriate security measures to protect patient privacy and prevent counterfeiting.
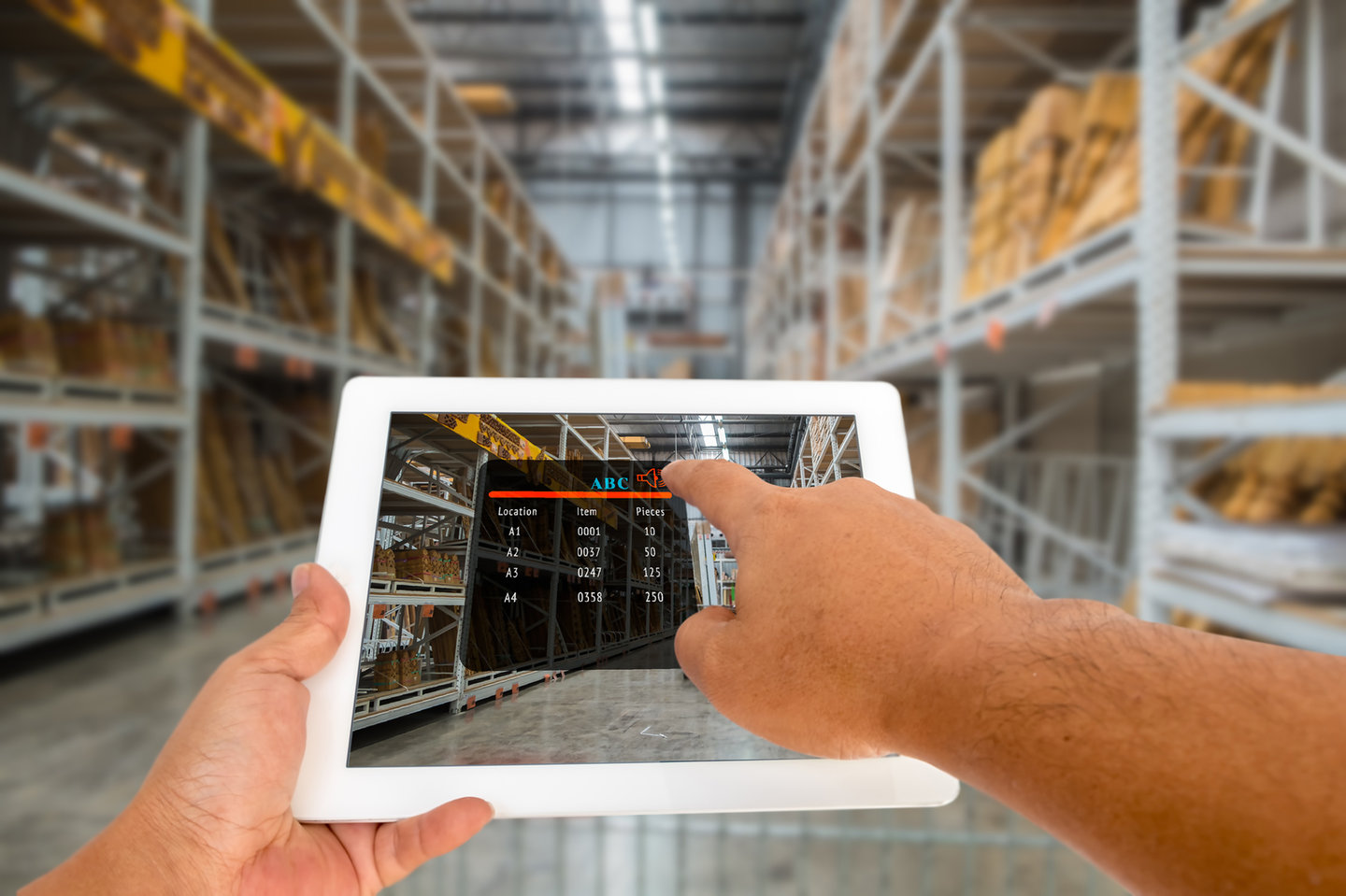
Credit: SHutterstock/ Montri Nipitvittaya