Company Insight
Sponsored by Nissei ASB Machine
Nissei ASB – Continuous Innovation for Demanding Markets
Polyethylene Terephthalate (PET) made its first impact on the container molding industry via carbonated soft drinks during the late 1970’s just as Japan’s Nissei ASB Machine Co., Ltd. was founded. In those early days only three machine manufacturers existed globally that produced equipment capable of stretch-blow molding this new material.
Mid-range One-Step Injection Stretch Blow Molding Machine – ASB-70DPH
ASB’S SOLUTION
was to design a 4-station, one-step injection stretch blow molding system where the raw material is converted into the final container within the same machine, a significantly different approach to two-step systems that require two separate machines plus additional handling and support equipment.
ASB’S SOLUTION
was to design a 4-station, one-step injection stretch blow molding system where the raw material is converted into the final container within the same machine, a significantly different approach to two-step systems that require two separate machines plus additional handling and support equipment.
The importance of innovation
While the two-step process can produce relatively simple shapes and low value containers at high outputs, it is basically limited to PET only. The great advantage of ASB’s one-step process is its ability to mold anything from the simplest container, right up to the highest specification and technically challenging containers, in complex and varied designs, and can be achieved at the highest possible quality, not only using PET but also a wide range of alternative plastic resins.
PET fares very well in terms of chemical resistance, impact resistance, toughness and visual appeal, plus ease of recycling, which has always been important, but more so nowadays than ever before. However, for specific applications other materials including Polypropylene, HDPE, PES, or Acrylic for example can surpass it, so a converter utilizing ASB’s one-step process has access to the highest degree of molding flexibility allowing them to most closely match their market needs.
This then is the reason why, even after more than 40 years, Nissei ASB remains as the longest serving player in the stretch blow molding industry, despite robust competition through the intervening years, the company remains by far the largest producer of one-step equipment and molds. This resilience has only been possible as a result of continual research into new techniques and molding processes that have shaped the industry as a whole and with the company having its name on over 1,800 related patents.
Beyond being just a machine and mold maker, ASB is continually promoting new patented container molding technologies and has been the pioneer of many now common industry features such as injected and inserted handles, pasteurizable PET jars, glass-like cosmetic containers and multi-layer molding. Not only has this led to an almost limitless potential for container design, it has also resulted in the ability to mold more than 20 resin types in addition to PET.
The pay off between food, safety and low carbon emphasises the need for innovation.
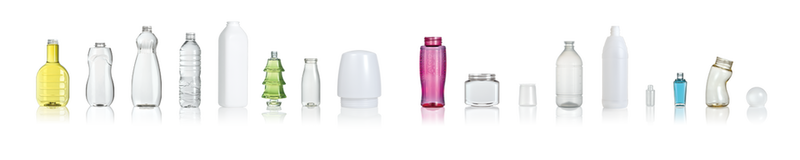
Just a small selection of the more than 20 resin types moldable by ASB's one-step ISBM machinesJust a small selection of the more than 20 resin types moldable by ASB's one-step ISBM machines
Working with policymakers to achieve demonstrable change
These diverse technology developments have helped the company to thrive and expand to now having five factories in two countries as well as local technical centers in Europe and the USA. The company established a global manufacturing unit near Mumbai in India in 1997 and in 2018, this facility was expanded to more than four times the original floor area with the addition of two new factories in 2013 and 2018.
To expand its global R&D facilities as well as domestic and East Asia manufacturing capacity, the Japanese manufacturing unit also saw a doubling in manufacturing floor space at the end of 2018 with the opening of its Chikumagawa factory in Saku City.
Nissei ASB’s turnover already accounts for around 15% of world-wide sales in all PET container production and with this expansion resulting in a total of 70,000m2 of global floor space, the company now has the capacity to produce up to 1,500 full mold sets and up to 700 machines annually.
Since the company produced its first molding machine over 40 years ago, the market has constantly put greater technical demands on packaging technology. Now, with growing pressures from social and mass media for a dramatic shift in the way we use plastics, the company is more than ever focusing on actively engaging with environmental protection organizations to promote the safe and responsible use and recycling of plastic packaging as well as developing new methods to combine the benefits of plastic containers together with environmental responsibility.
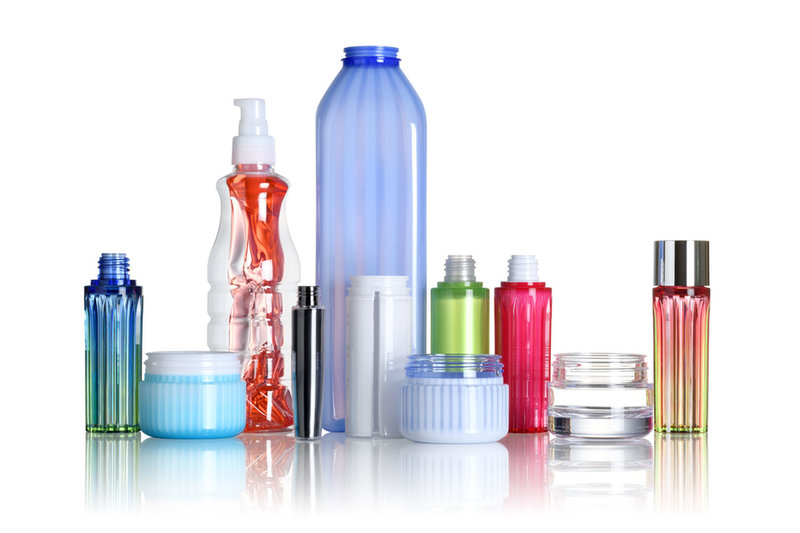
Double layer molded containers provide a range of environmental, technical and aesthetic advantages
For example, one recent development has focused on molding the preform in two separate injection steps to create two distinct layers that can be used to provide food-safe containers molded with high percentages of recycled materials that also protects the environment, or can be used to enhance shelf life for food products, or create premium aesthetic containers with enhanced marketing appeal for cosmetics.
Today, the founder, Mr. Daiichi Aoki still heads the company which, in a growing world of faceless corporations, remains as an independent organization that brings a sense of family to its staff and customers alike while remaining at the forefront of the container injection stretch blow molding industry.