Digitalisation
Harnessing the benefits of digitalisation
Digitalisation allows packaging manufacturers to achieve mass customisation, but financing new technology is a key challenge, say Carolyn Newsham and Kirsty Talmage-Rostron, UK business development managers for industrial equipment at Siemens Financial Services.
Image: Siemens
Image: Siemens
The value of customised packaging
There is extra pressure on packaging producers as the importance of packaging to consumers continues to increase. Consumers are bombarded with more and more product variations and packaging plays an important part in attracting attention and building a brand.
Technology now allows packaging to be customised so that it precisely targets audiences and markets. This inevitably means more variation, more SKUs, which requires greater flexibility, shorter runs and shorter turnaround times, which digitalised processes can achieve.
Several soft drinks brands have demonstrated the value that customised packaging can bring. For example, Coca-Cola launched ‘Meine Coke’, which allowed customers to personalise their own labels by entering their desired label text online.
In 2018, Danish mineral water brand Aqua d’Or used digital printing technology and an artist’s designs to create millions of labels carrying unique graphic patterns for its bottled water.
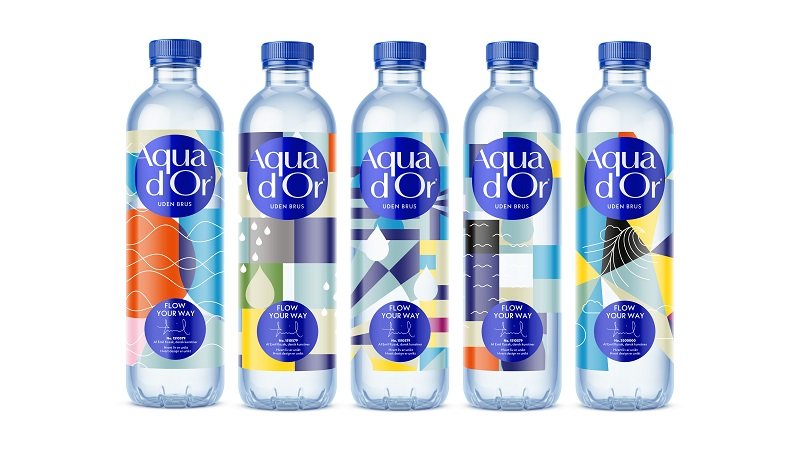
Aqua d’Or’s unique labels from 2018. Image: Aqua d’Or.
These examples of “mass customisation” show how digitalised Industry 4.0 print and dispatch technology are helping brands to build their image and customer relationships. This idea of bespoke packaging is being taken even further by a beer company that has used augmented reality to create a label that “talks” to the consumer.
When the smart label is scanned using an app, facial recognition technology actively incorporates the consumer in dynamic scenarios according to the emotions displayed. The technology recognises whether the customer is happy or sad and the label-based dialogue with the consumer is adjusted accordingly.
Improving efficiency
As well as providing opportunities for clever marketing, digitalisation in the packaging industry also helps improve efficiency during conception and production. Data analysis can help to reduce machinery downtime and increase production capacity at the same time.
Packaging and displays can be developed online, with their size and material precisely calculated before they are transferred to physical substrates such as glass, sheet metal, paper or plastics using 3-D tools. Designers, managers and manufacturers can collaborate virtually on databases, while the data stored in the cloud is accessible for all project participants, improving co-operation and efficiency.
There is a range of other applications that players in the industry can capitalise on, including active and intelligent packaging that embeds radio-frequency identification (RFID) chips; tracking print technology to meet regulatory requirements for traceability; the just-in-time movement of goods through intelligent packaging print that can, for instance, monitor and manage cold chains in the food industry; cloud linkage between customers and producers that helps improve the customer experience by bridging digital and physical interactions, and more.
However, financing the investment of this technology is a key challenge for many packaging manufacturers. That’s why many manufacturers are now embracing financing arrangements which enable them to invest in new equipment and technology with confidence. Pay-to-use and pay-for-outcomes agreements are effective alternative methods of funding equipment and technology investments and upgrades.
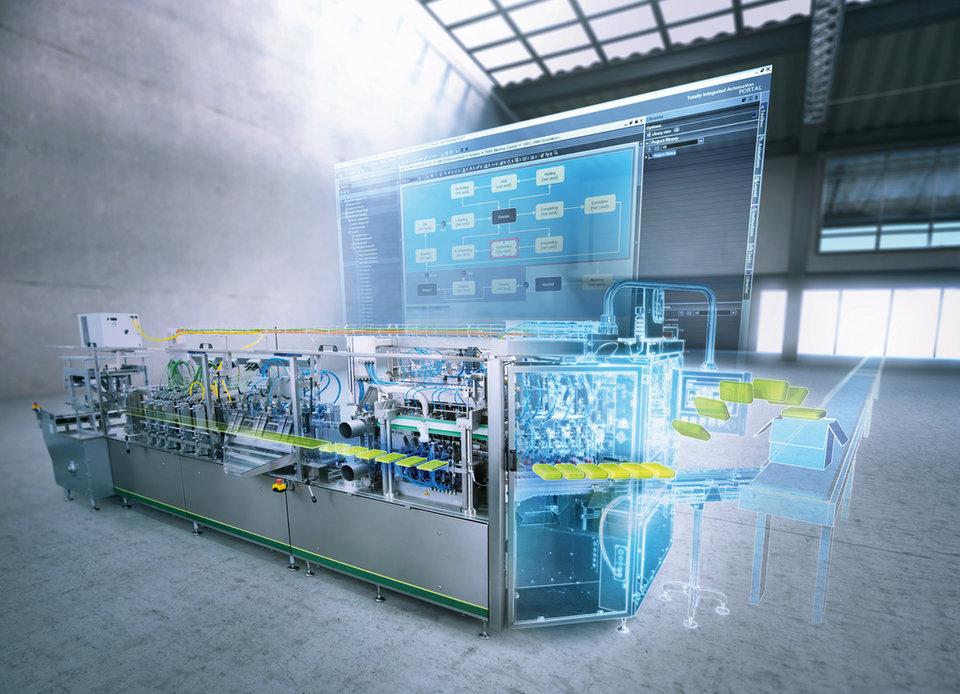
Financing the investment of this technology is a key challenge for many packaging manufacturers. Image: Siemens.
Such financing techniques spread the cost of technology over an agreed financing period, whereby the customer’s monthly finance payments can be aligned with expected benefits gained over time from new/retrofitted equipment, such as improved productivity, operating cost savings, energy efficiency and access to new markets. This removes the need for a large initial outlay and leaves existing funds available for other expenditures.
In other words, asset finance enables manufacturers to access the latest technologies without having to commit scarce capital or use traditional lines of credit. Financing arrangements can also cover other costs such as installation, as well as provide flexibility to upgrade technology in line with developments.
Unlike traditional, generalist financiers that might lack the comprehensive technical knowledge to fully evaluate the impact a potential investment can bring to a packaging producer, specialist financiers active in the manufacturing arena understand the technology, its potential future value and its practical application.
By using flexible financing, manufacturers have the opportunity to benefit from the investment in equipment and technology straight away.
This comprehensive understanding of the financed equipment and technology enables specialist financiers to determine appropriate and tailored financing solutions that meet the customer’s specific needs. Their expertise in the equipment to be financed makes it possible for specialist finance providers to assess the cost savings and/or expected benefits for the term of the agreement and factor that into the financing arrangement.
Moreover, they can devise financing plans that cover a broad range of costs associated with using the equipment and technology, not just the cost of acquisition, meaning greater transparency regarding the expected operating costs for the customer. By using flexible financing, manufacturers have the opportunity to benefit from the investment in equipment and technology straight away rather than delaying their acquisition, and through that timely investment gain an important competitive advantage.
There are many benefits digitalisation can bring to manufacturers in the packaging industry. Even in times of economic turmoil, these companies must keep up with developments, or they risk losing ground to competitors. Partnering with a financier that understands the industry can help them on the path to digitalisation while protecting the all-important bottom line.
T
The economic impact of Covid-19 is touching every industry, and packaging is no exception. Packaging companies are under pressure to embrace digitalisation and automation, particularly as technology continues to develop apace.
Siemens’ research shows that, in the manufacturing industry as a whole, the “tipping point” of Industry 4.0 adoption - defined as when 50% of the global manufacturing community will have substantially converted to Industry 4.0 production platforms - will be reached within the next five to seven years for larger manufacturers and around 10 years for SME manufacturers.
More importantly, early movers – the first 50% of players to invest in new technologies or business models – are those that will be able to make the most of this competitive advantage, at the expense of competitors that have not adopted.