Company Insight
Sponsored by Nissei ASB
Nissei ASB - Pioneering Packaging Technology
Since its founding in 1978, Nissei ASB Machine Co., Ltd. has remained the world leader in 1-Step injection stretch blow molding technology for production of PET, and other plastic container packaging for virtually any product from foods and beverages through to cosmetics and toiletries, or household supplies and industrial chemicals.
At CANPACK, we are convinced that exceptional products deserve exceptional packaging. In the spirit of the saying "differentiate or die", manufacturers and brands cannot afford mediocre product packaging. This is why, in order to create and maintain long-term consumer awareness, it is crucial to look for packaging ideas that will allow products to shine on the crowded store shelves.
Beyond being just a machine and mold maker, ASB is continually promoting new patented container molding technologies and has been the pioneer of many, now common packaging features such as injected and inserted handles, pasteurizable PET jars, glass-like cosmetic containers and multi-layer molding.
Injection stretch blow molding maximizes the properties of PET material through biaxial orientation leading to the lightest weight and most efficient form of container packaging having the lowest possible carbon footprint, while the PET resin itself is universally recyclable either back to containers or to a wide field of alternative uses including clothing and carpets.
Globally, two major molding techniques are used known as either the 1-Step or 2-Step process, but whichever is used the fundamentals are the same. A preform is manufactured by injection molding where the neck shape is finalized, with the body being about 10% or less of the final container volume. The preform body is then temperature adjusted to around 105°C for final stretch blow molding to be conducted.
In the 2-Step method, each part of the molding process must be conducted on separate machines, requiring full cooling and reheating of the preform as well as interim preform storage and handling between the two molding operations. Depending on the requirements, a molding company may need to source suitable preforms from the global market or may need to set up their own preform manufacturing unit.
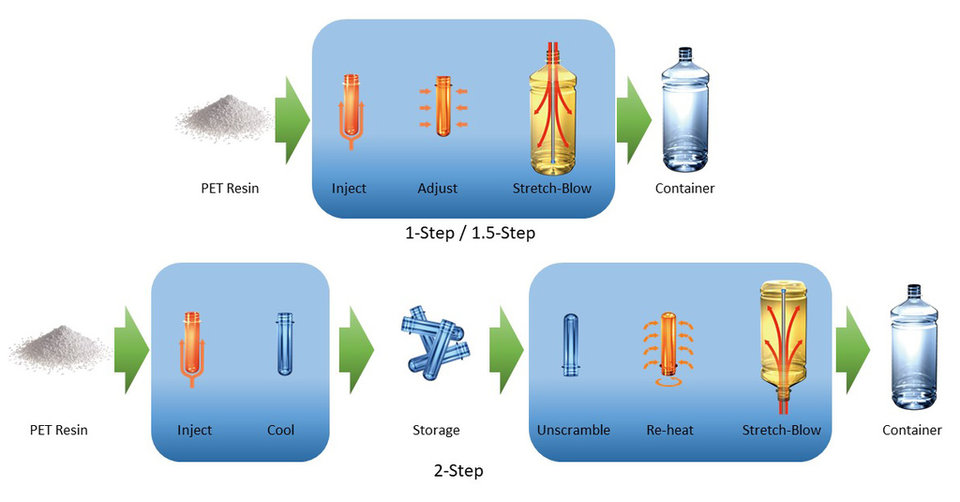
1-Step molding vs 2-Step molding
In the 1-Step method, raw material can be converted directly into the final container in one machine resulting in a highly compact system requiring no preform handling or storage. Since the preform is manufactured within the same machine, its design can be readily customized to suit highly technical or premium container designs, while its quality remains uncompromised.
Broadly speaking, 2-Step technology is efficient for very large-scale production of low value containers such as water, soft drinks and other relatively simple shapes. Meanwhile, 1-Step technology can mold literally any container design or specification available by the 2-Step process, but has the additional capability of molding any diverse types that are beyond the scope of 2-Step for markets such as household, toiletries, cosmetic and industrial products.
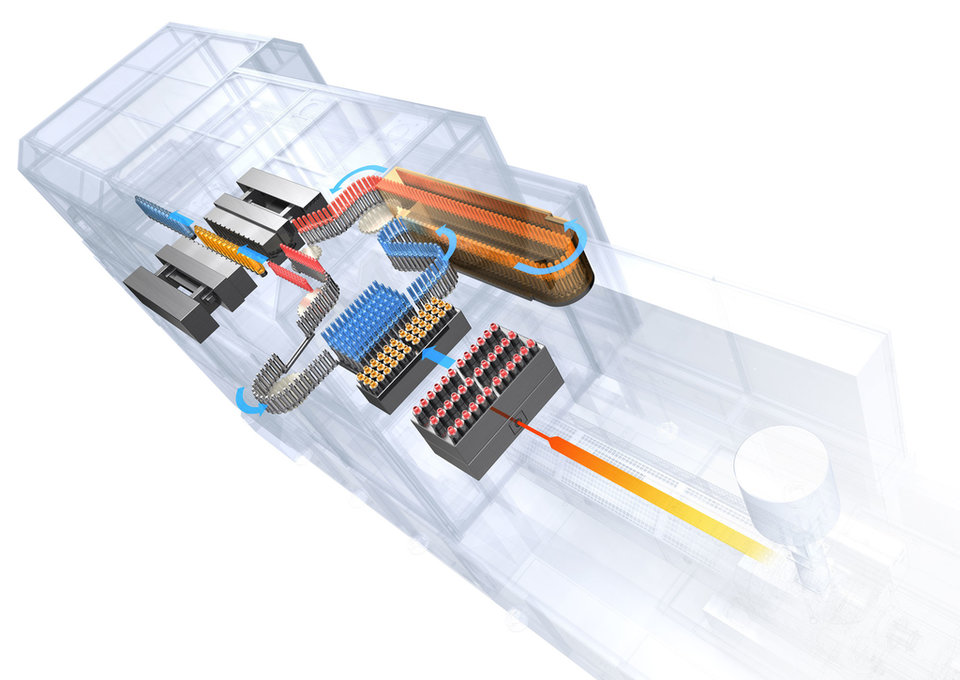
PF36 Series 1.5-Step Injection Stretch Blow Molding Flow
Conventional 1-Step systems tend to have lower output per machine, so ASB developed the 1.5-Step process used in the PF36 Series machine to provide higher outputs suitable for typical in-line filling operations, while still maintaining the compact, efficient and high-quality benefits of the 1-Step process. Even with lower output, installation of multiple machines can easily match filling requirements while still retaining a simpler production process, reduced floorspace and higher control of quality – or, if required line flexibility for product shape and size.
The PF36 Series molds PET bottles in a range of sizes from 100ml up to 5 liters. Output efficiency is optimized by setting the mold cavities according to container size and weight using 36, 24, 18 or 12 with smaller containers being available in greater cavities.
In two major water filling line projects, ASB recently secured contracts by offering multiple units of PF36 machines where the total investment cost was found to be significantly lower than an equivalent 2-Step installation, while the required floor area was just 25% of the competitor. Multiple molding machines also gave each customer the flexibility to adjust the output balance of separate product lines seasonally.
It is this diversity and flexibility that has resulted in continued growth in the 1-Step segment in recent years. As of 2018, ASB’s Indian facility has expanded to more than four times the original floor area with the addition of two new factories in 2013 and 2018, with the former being 100% dedicated to mold design and manufacture.
To expand its global R&D facilities as well as domestic and East Asia manufacturing capacity, the Japanese manufacturing unit also saw a doubling in floor space at the end of 2018 with the opening of its new Chikumagawa factory in Saku City.
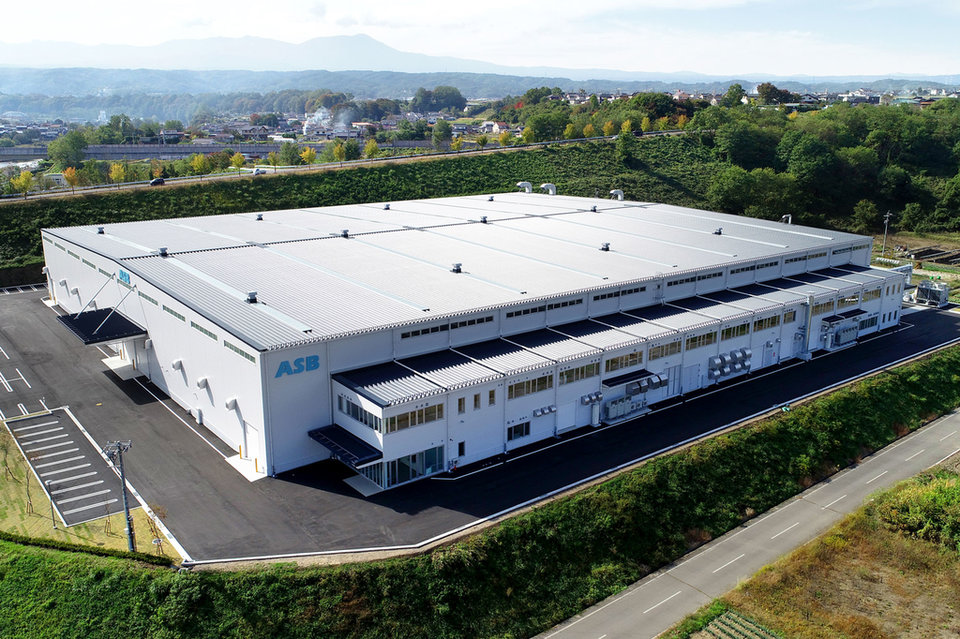
ASB's Chikumagawa Factory - Japan
Nissei ASB’s turnover already accounts for around 15% of world-wide sales in all PET container production and with this expansion plan resulting in a total of 70,000m2 of global floor space, the company now has the capacity to produce up to 1,500 full mold sets and up to 700 machines annually, while future growth looks set to require additional expansion.
A worldwide network of 16 sales and service subsidiaries and a further list of over 40 sales agents that completes global coverage and ensures that ASB customers in over 130 countries are never far from sales or technical support.
Main Image: PET containers from the PF36 machine - 100ml up to 5 liters