The new generation dryer for rPET
GenesysNext represents the state of the art in drying systems for preform, creating a new standard. The cost for good preform produced is now reduced to a minimum level considering the main advantages: minimum waste of material due to scrap, lowest energy consumption and minimum labour cost, since the system is fully automatic.
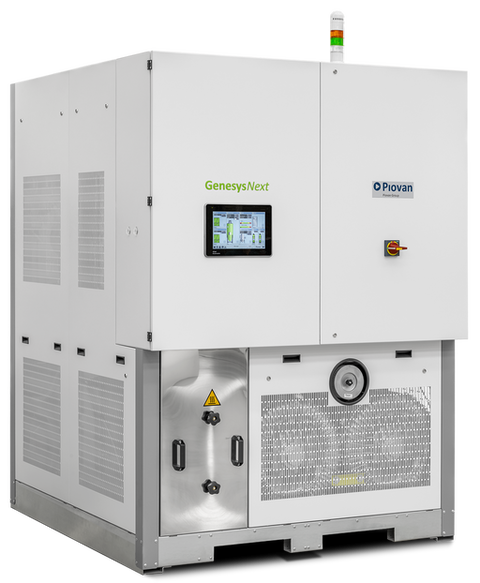
PETperformance, is a system to minimize scraps rate. Introduces for the first time the concept of a direct connection between drying and injection process, thanks to it, GenesysNext is capable to read the injection pressure and to stabilize it, reducing the scraps rate.
PureTech is a system to process any kind of rPET. Is the new filtering system to remove the contaminants that can be accidentally present in the recycled materials and that can be released during the heating phase, to guarantee the higher quality of the preforms produced.
Material traceability to keep the process under control. The new advanced control of GenesysNext allows the recording of all the main process parameters and trends, like process air temperature, DewPoint, final humidity content of the resin, airflow, among others and link them to the lot of material processed.
Full integrated solutions for the smart factory
Piovan Group can provide a complete turn-key solution for a PET preform bay production, and GenesysNext is the key point of the system.
The new powerful control, for a higher level of data elaboration and process control, can manage the complete bay, including the mould dryer, PETchiller, dosing units, Ryng and centralized feeding system. GenesysNext integrates also the data of the injection pressure and humidity content of the resin, thanks to the Moisture Minder.
GenesysNext is a smart machine designed according to Industry 4.0 principles: the process blower frequency control is fully integrated, the desiccant towers temperature profile is fully monitored, the process airflow is controlled by and advance algorithm or the filters are equipped with a detection system for clogging, all these allow a real-time diagnostic and the scheduling of the preventive maintenance.
The optimization of the energy consumption has gone even further with a new airflow distribution in the desiccant towers to improve absorption capacity and the updating of the regeneration circuit to increase heating recovering.
110+ Counties Served
1.300+
PET Systems Customers
5.500+
PET Drying systems installed
Crystallising systems make possible the processing of amorphous material, in the form of flakes or chips. The low speed shaft reduces friction and dust generation. The crystallising step provides also a pre-drying and pre-heating of the material, reducing the drying energy consumption.
Piovan Group has a complete range of vacuum receivers for flakes, with features specifically designed for critical and light materials such as a dedicated geometry, pneumatic flap, bridge breaker and level sensors. Varyo, the technology for managing the speed of the material during conveying phase, minimize the creation of dust. The reliability of the feeding systems is guaranted even in case of highly dusty materials thanks to a set of cyclone and cartridge filters with or without automatic cleaning.
The CDF condensing units provide an additional filtering step and make possible the condensing of low boling contaminant substances. The cooling water consumption is optimized thanks to EMK automatic valve and the maintenance is easy with the removable filters and heat exchangers, quick couplings for water connections and separate collecting bin for condensed materials.
Any kind of materials or scraps can be reprocessed thanks to the right granulator. There are dedicated solutions to grind components made of different raw material, with different size and coming from different applications such as thermoforming skeleton, strapping band, profiles or pipes, bottles and pre-forms.