company insight
Since
Xeikon Pre-press joined the Flint Group Family in 2015 both Flint Group Flexographic and Xeikon Pre-press were suddenly in the very unique position to have the expertise in plate manufacturing and plate processing equipment in-house. This unique position in the industry resulted in a close collaboration between our R&D departments with the aim to provide a fully optimized Pre-press environment to our customers including equipment and plates. "We believe that no one in our industry can match this level of expertise and the first feedback we got from our beta customers is confirming our view", says Friedrich von Rechteren, Global Commercial VP, Flint Group Flexographic.
Xeikon Pre-press R&D Director Bart Wattyn explains: “Right from the beginning our ThermoFlexX imaging systems were designed to help our customers through automation and leading edge technology. By listening to the challenges our customers have to face every day, like handling large size flexo plates that are easy to damage, we developed the Flextray with fully automatic loading and unloading. The positive feedback we received was tremendous! Consequently, we announced the Catena-E LED exposure system in 2019 with a fully automatic plate feed from our imagers. Plate processing (wash-out) gives an extra challenge and we took it as a design goal that an operator should be able to handle large plates, single handed and without ever having to come into contact with their solvent-wet surface”.
The later additions to Flint Group’s Catena Product family, the Catena-W , for Washer, and Catena-DL, for Dryer Light finisher, follow Flint Group’s promise of delivering solutions which are Better.Faster.Easier to use.
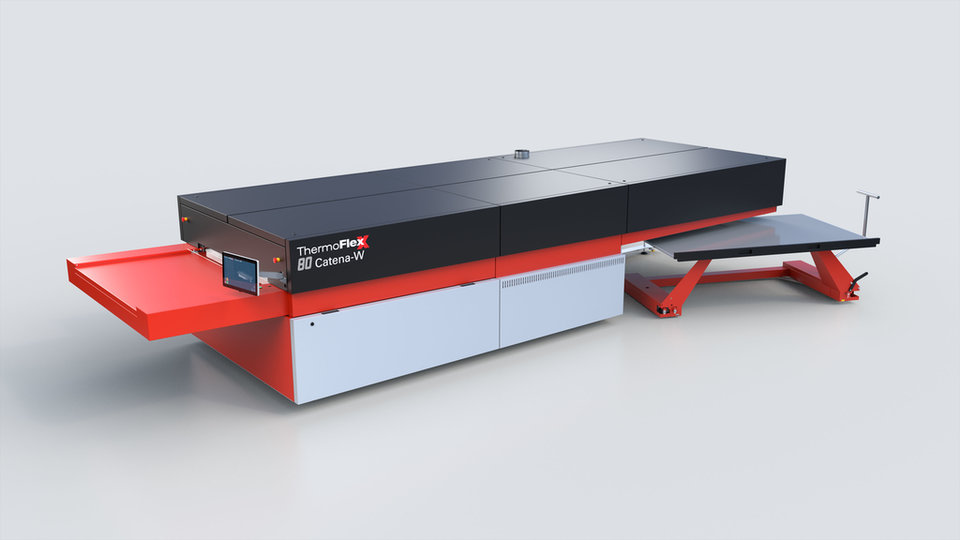
Catena-Washer
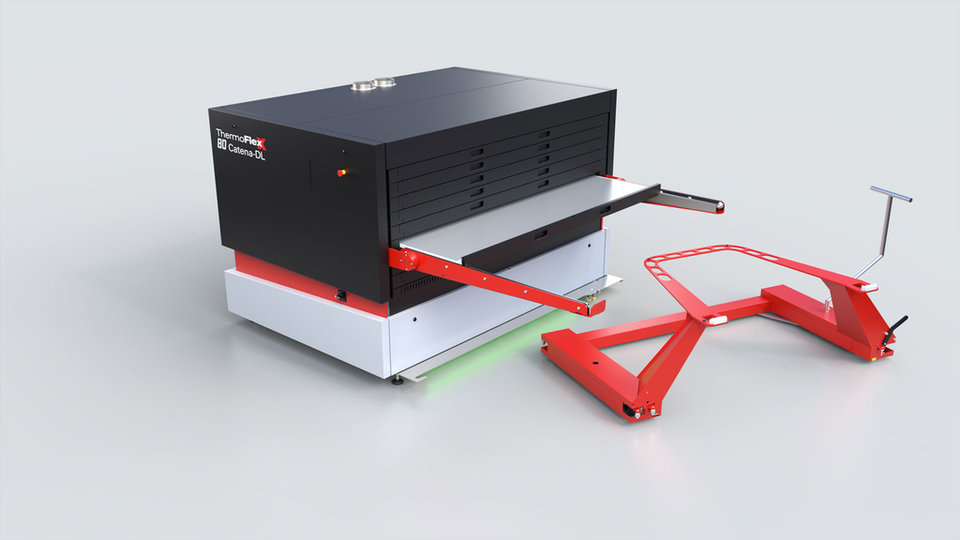
Catena-Dryer Light finisher
The Catena-W is designed to deliver highest productivity through unique plate alignment which avoids plate skew during transport as well as an advanced plate queuing system. This limits the distance between plates being processed and maximizes the throughput. Compared to other washers the Catena-W operates in a sealed environment. Its efficient extractions ensure a minimum of solvent fumes reaching the workplace, which benefits the health and safety of operators.
The Catena-DL features an automated lift that can be used to move a plate from the shuttle to the dryer drawers and into the light finishing section while avoiding any human touch point.
The newest announcement of fully automated flexographic plate processing equipment, The ThermoFlexX Catena+ brings the whole chain together, resulting in leading edge fully automated flexo plate making. Once the operator has removed the cover sheet the plate is automatically loaded into the imager, and is completely processed and fully finished with no further operator interventions needed, eliminating any damage caused by manual plate handling.
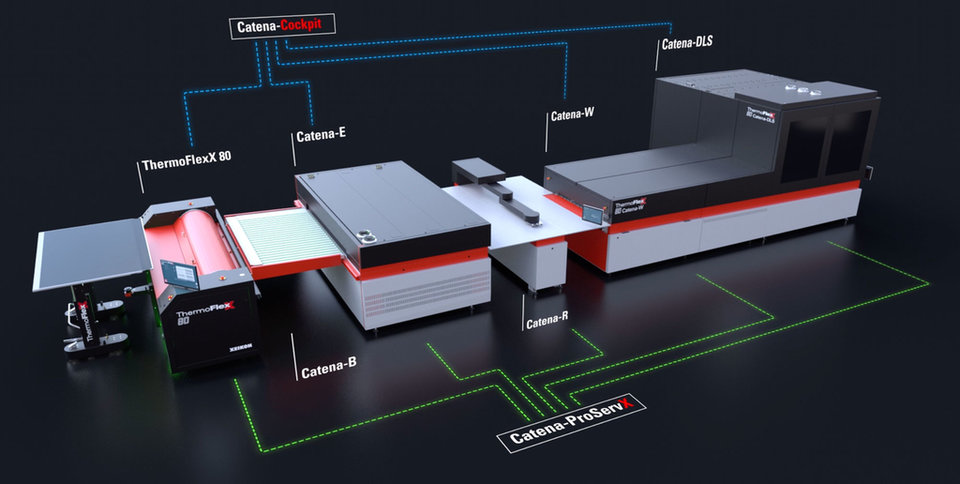
Catena+
“We are proud to announce the Catena-DLS, the missing piece on our way to fully automated flexo plate processing. We provide a state-of-the-art, fully automated and integrated flexo plate processing system, which allows our customers to produce flexo plates at lowest total cost for every application“, explains Uwe Stebani, General Manager Xeikon Prepress. “And in combination with our groundbreaking ThermoFlexX Woodpecker surface screening software and best-in-class Flint Group flexographic plates, we enable our customers to rival any other system in the market.”
Designed as an open system, Catena+ allows easy loading of plates from other imagers into the Catena-E LED exposure unit. Plates from other exposure frames can also be easily loaded to take advantage of the highly productive WDLS.
The full line Catena+ also includes Catena Cockpit, which provides a highly visible status report on plate processing, progress and expected time of completion. With Catena ProServX software, the machine health status of all modules is constantly monitored, thus, enabling a new level of pro-active support and maintenance. The need for physical service-interventions is minimized.
For more information on the ThermoFlexX TFxX imagers and Catena equipment, please visit our website www.ThermoFlexX.com.