COMPANY INSIGHT
Sponsored by Nissei ASB
Nissei ASB – Container Molding Versatility
Since its invention by Nissei ASB Machine Co., Ltd. in 1978, the 1-step injection stretch blow molding process has led the industry in versatile production of high quality, unique and specialized bottles and jars in PET, and other plastics including those that help protect our environment.
Although its primary market is food, beverages, and daily life products, the versatility of the one-step ISBM process enables all manner of containers to be molded including glass-like cosmetics, industrial products, pharmaceutical and life-saving medical containers - all the way through to non-packaging products such as lamp covers, automotive and office equipment. Moldable resins include PET, PP, HDPE, and more than 20 others including bioplastics and biodegradables.
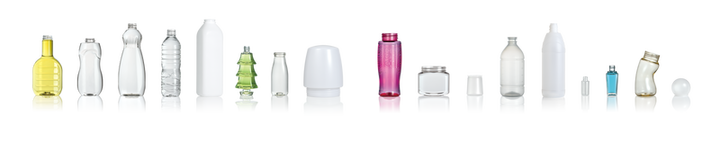
A multitude of product shapes and molding resins are possible
For molders operating conventional 2-step reheat PET stretch blow machines, required preforms will either be purchased from external suppliers or manufactured in-house on separate injection molding machines followed by interim preform storage and handling before blow molding. In either case, design availability, practicality of automated handling or the reheating process itself place many restrictions on the container designs, especially in the neck and shoulder region.
In the 1-step method, raw material can be converted directly into the final container in one machine resulting in a highly compact system requiring no preform handling or storage. A full mold set for the 1-step molding process includes all parts required for injection molding, preform conditioning, and stretch blow molding resulting in three significant advantages for container design and quality;
- The preform is custom molded precisely for the container - there is no limit on design parameters due to interim handling.
- After injection molding, the preform is transported through the rest of the process while securely held by the same neck parts that formed it, eliminating any risk of damage.
- Retained heat from injection molding allows designs or resins that cannot practically be reheated.
Today, no other manufacturer in the market can provide such a wide variety of stretch-blown container molding solutions. Beyond being just a machine and mold maker, ASB is continually promoting new patented container molding technologies and has been the pioneer of many, now common packaging features such as injected and inserted handles, pasteurizable PET jars, glass-like cosmetic containers and multi-layer molding.
Its signature line-up of ASB-Series machines includes ten models tailored to almost any container molding scenario from 5ml up to 20 liters, molding 1 to 48 cavities arranged in 1, 2 or 3 rows, providing outputs from 50bph up to 20,000bph.
All ASB Series 1-step models are fully capable of molding basic PET bottles for mineral water or soft drinks at mass production rates, but with their overwhelming versatility, their forte is the molding of containers having higher technical, market-appeal or quality demands with little to no restrictions on design or molding resin. Alternatively, smaller models in the line-up can be utilized as a product development platform, or multiple units can be installed for incremental production growth.
The 1-step process provides incredibly compact molding with the larger, high output models consuming only about 30% of the floorspace required for a similar output 2-step production line.

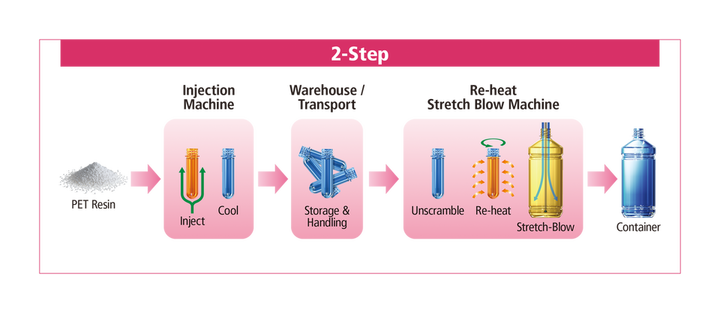
1-step molding vs 2-step molding
Molding processes are carried out simultaneously in four stations. First, the raw material is melted and injected into the preform mold while undergoing partial cooling. After injection, the still hot preforms are transferred to the second station where various specialized processes can be applied.
Using ASB's patented Zero Cooling™ process, most PET containers can benefit from an average of up to 30% reduction in cycle time while providing improved quality, strength, and the opportunity for additional weight reductions. Alternative resins and certain PET designs may instead benefit from the use of ASB’s unique preform conditioning system consisting of customized mold parts to heat or cool sections of the preforms for optimum blowing.
The prepared preform then moves into the blow station where stretch blow molding is conducted. Again, a variety of techniques can be used to produce unique or specialized, high value products as well as all common designs.
At the fourth and final station, molded containers are ejected for packing or downstream processing and the now, empty lip cavities return to the injection station.
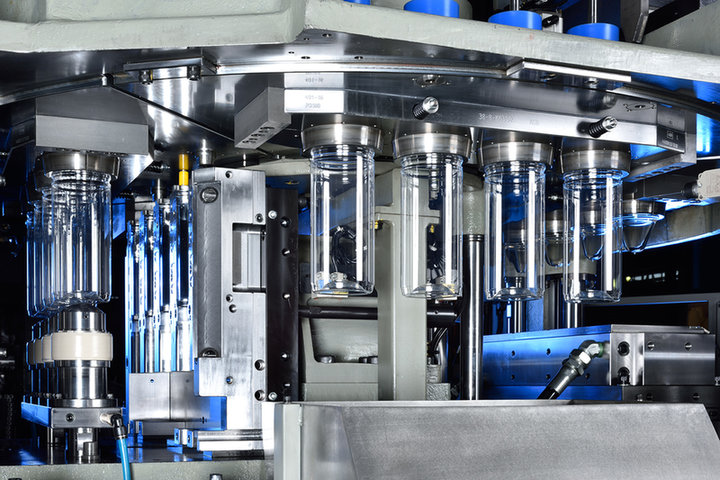
Finished PET jars at the eject station of an ASB-70DPH machine
ASB is the world leader in 1-step stretch blow molding, its turnover accounts for 15% of world-wide sales in all PET container production. A network of 16 sales and service subsidiaries and a further list of over 40 sales agents completes global coverage and ensures that ASB customers in over 130 countries are never far from sales or technical support.
Although ASB’s focus is on the 1-step market, the company also makes a wide range of package molding machinery including;
- High efficiency and compact 1.5-step PET bottle molding (PF Series)
- PET preform molding (PM Series).
- Neck Crystallizing for heat resistant containers (CM Series)
- 2-step re-heat stretch blow molding machines for heat resistant / returnable & refillable containers. (HSB Series)
- Injection machines for handles, caps and all other types of general-purpose injection molding. (AIME Series)