COMPANY INSIGHT
Wake up to better coffee packaging
Coffee consumption is expected to continue to grow over the next two years and many ground coffee manufacturers
are seizing this opportunity by expanding their production. Packing this valuable product as quickly and accurately as possible is a challenge. Bosch’s efficient solution makes it an easy one.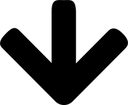
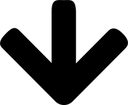
How the right packaging solution can help ground coffee manufacturers double output and improve efficiency
When dealing with a valuable product such as coffee, packaging can contribute to significant product savings or losses, by just a few grams at a time. By adding extra product to their bags, some manufacturers err on the site of caution, so they don’t risk consumer trust and brand reputation. Of course, this impacts their margins: adding an extra ten gram per 250 gram bag, for example, means they are giving every 26th bag away for free.
Accuracy versus speed is a trade-off for which the industry has long been waiting for a solution. Thanks to continuous improvements of the technology, vertical packaging systems can now address this challenge better than ever – producing up to 300 fractional coffee bags per minute on minimum floor space while ensuring high filling accuracy.
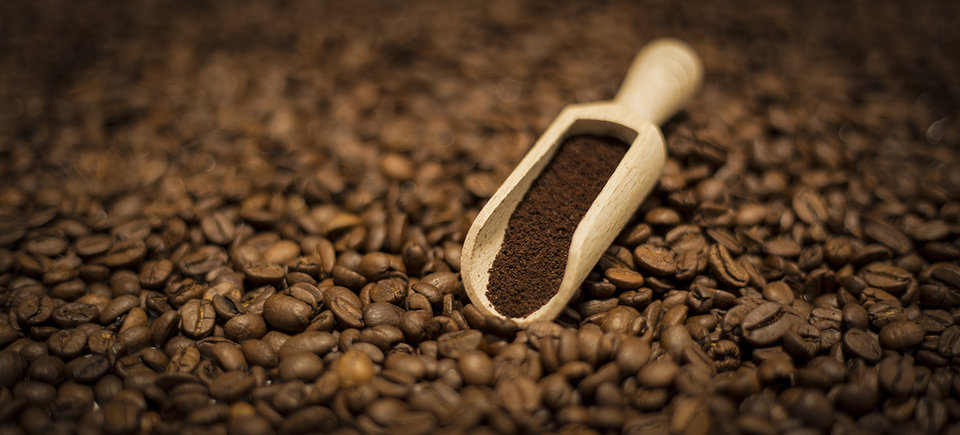
Optimize your ground coffee production by choosing the right packaging solution
Look for small but mighty: go vertical
As the name suggests, vertical packaging systems can help save valuable floor space thanks to their set-up: a roll of film is formed into a bag, filled with product, and sealed; all in one continuous, top-to-bottom motion. While this is a simplified explanation, vertical packaging machine systems have several advantages for ground coffee manufacturers.
Designed properly, they are particularly cost-effective, supporting product and material waste reduction, and simplifying cleaning and maintenance at the same time. One great example is the unique combination of Spee-Dee’s 3600 Twin auger filler and Bosch’s SVE 1820 MR continuous motion bagger. This duplex machine – first introduced in the U.S. early this year – fits on just 3.4 square meters, doubling production output on a fraction of the space compared to previous generation of machines. Unlike some competing solutions, it does not imply a sacrifice of filling accuracy, bag quality or bag quantity: it produces up to 300 consistently airtight bags per minute, with a maximum bag width of 180 millimeters – the largest possible bag width for a duplex machine. That means that coffee manufacturers can produce a wide range of bag sizes – with up to 250 grams per bag.
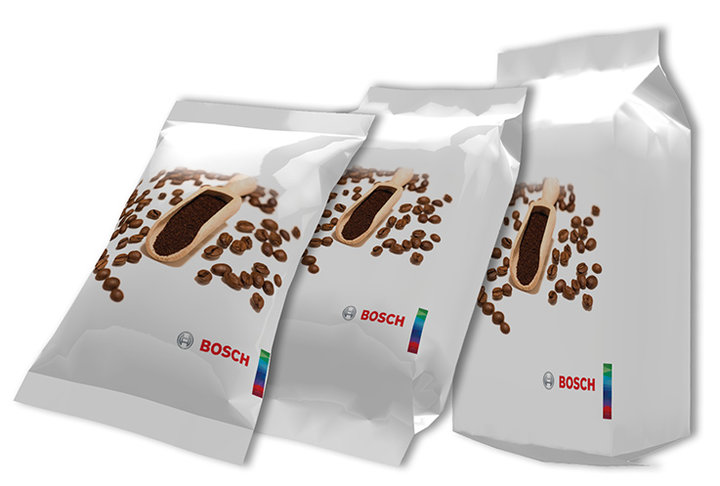
Quality and quantity can go hand in hand – with the unique combination of Spee-Dee and Bosch equipment for ground coffee
Don’t waste a single gram: choose the right filler
As even the slightest margin of error can mean a substantial loss of product – and revenue – for coffee manufacturers, current solutions like the Spee-Dee auger filler offer unparallelly high filling accuracy. This is achieved through tendency regulation with a checkweigher, cutting product waste and eliminating the need for adding extra product. At the same time, a single hopper inlet should simplify the upstream product delivery system; just like the combination of Spee-Dee’s auger filler and Bosch’s SVE 1820 MR.
Stay flexible: maximize product and material range
Additionally, ground coffee producers routinely need to switch from decaf to regular or flavored product. Therefore, the ideal packaging solution should also feature a sliding key tooling lock for effortless changeovers and tool-less hopper changeovers to reduce downtime and minimize cross-contamination risk. Easy cleaning, maintenance and monitoring thanks to an open vertical form, fill and seal (VFFS) machine design improve overall equipment effectiveness even further.
Furthermore, high-quality seals need to work with various film materials so coffee producers can choose between two- and three-ply films without compromising on sealing quality. The unique solution of Bosch and Spee-Dee equipment offers just that – and on a fraction of the floorspace no less. Customers also profit from nitrogen flushing – which extends the product’s shelf life – an optional feature of flexible solutions like Bosch’s SVE 1820 MR, which can be further enhanced with a double film reel carrier and carrousel, labeler and printer systems or product jam detection.
Coffee manufacturers looking to tick all of these boxes can learn more on solutions4value.com or schedule an informal session in the Bosch customer solutions center in Weert, the Netherlands.
To claim your free exclusive slot to speak to the experts one on one, email systemsolutions@bosch.com , mentioning that you heard about this opportunity through “Inside Packaging – Coffee 2018”.
Contact Information
Bosch Packaging Technology
Website: solutions4value.com
Email: systemsolutions@bosch.com