Newly developed NDF gearbox with flanged output from Neugart
Feel free to contact us:
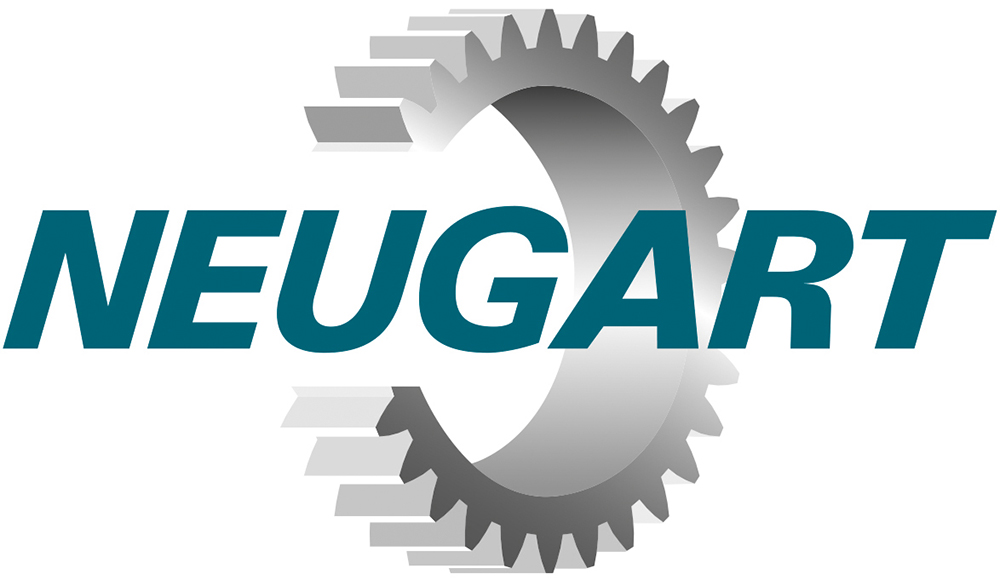
Dynamics and precision for Delta robot drives
Several hundred movements per minute, with high precision and in a small space: Delta robots achieve extraordinary results. That also applies to their drives. Planetary gearboxes offer specific advantages, as Neugart is currently demonstrating with the application-specific, newly developed NDF.
Whether in the food and pharmaceutical industries or in many other sectors: Where fast and precise handling steps need to be automated, Delta robots offer an ideal solution. For example, in packaging system or in logistics centers, they perform a wide range of pick-and-place tasks. They pack chocolates, sort packages or assemble printed circuit boards hundreds of times a minute.
This is made possible by the characteristic kinematics of this robot type: All axes of its rod-based robot arms are arranged parallel. The ends of the arms, which can move in all directions, are connected by a small platform that supports a suction cup, for example.
Since the drives are not located in the joints, the arms in Delta robots are extremely lightweight. This means that only a small amount of mass has to be moved, which enables high speeds and great dynamics with very high acceleration.
Special drive requirements
As a consequence, the reduced load resulting from the design of the robot arms means that the servo motors of the main drives and, with them, the gearboxes that connect them to the robot arms are subjected to extreme loads. They have to work dynamically with extreme precision and constantly changing directions of rotation.
Planetary gearboxes in which at least three gears (planet gears) revolve in a ring gear around a hardened central gear (pinion or sun gear) are generally well suited for this task. Because several gear teeth (depending on the number of planets, six or more) are engaged simultaneously in a planetary gearbox, such gearboxes offer the highest efficiency of all gearbox types, an extremely high transmissible torque in a very compact design, and thus a high power density.
NDF as a powerful solution
However, in order for the advantages of a planetary gearbox to be fully exploited in Delta robots, some special modifications are necessary in the gearbox design. These relate in particular to maximum torsional stiffness (torsional rigidity), minimum torsional backlash, reduced inertia, low breakaway torque and a modified sealing concept.
With its new NDF gearbox with flanged output, Neugart shows what such a powerful solution can look like. It has, for example, a very torsionally stiff planet carrier cage and specially designed planet gears. As a standard feature, the torsional backlash of the gear teeth is limited to less than 1 arcmin. As a result, the positioning accuracy of the robot is correspondingly high. This reduces readjustment of the system to a minimum and shortens the robot's cycle time. In addition, the NDF is characterized in detail by a whole series of other special features at both the input and output.
Construction features at the input and output
For example, in the input stage an aluminum clamping ring reduces the inertia of the clamping system. A low-friction radial shaft sealing ring also reduces the breakaway torque. This "Dynamic Drive System" enables extremely fast direction changes and at the same time reduces the load on the motor. Thus, less power is required to drive the gearbox. This allows a smaller and lighter motor to be used.
As a further measure, three planetary gears are installed in the input stage of the NDF, which not only keeps the inertia low but also reduces friction at the high-speed input stage. This means that the gearbox is subjected to less heat. Less heat is generated, especially at the rapidly rotating gearbox drive. Furthermore, splashing losses in the oil bath are reduced.
The three planetary gears at the input have as their counterparts four planetary gears in the output stage.This significantly increases the torsional stiffness and the transmittable torque. In addition to increased dynamics, positioning accuracy and cycle time, the control quality of the drive as well as speed and precision when approaching the target point are also improved.
A special radial shaft sealing ring (RSSR) is used at the output as well. It is designed specifically for the difficult lubrication situation, as the gearbox output shaft on Delta robots never rotates back and forth by more than a few degrees in application, making lubrication more difficult. The RSSR used also exhibits optimized flexing behavior during rapid changes in direction of rotation, thus ensuring optimum shaft sealing reliably over the long term.
The flanged output shaft with torque interface has 12 threaded holes (M6), the output flange has 16 holes (instead of the standard eight for each). The stiffness of the interface connection thus increases and higher torques can be transmitted.
Sizes and further options
The NDF is available in size 090 and with a total of four two-stage transmission ratios, each between i=22 and i=55.
A food-grade oil lubrication system is available as an option for the NDF. The lubricant used is certified to NSF H1 and ISO 21469. As a further option, the NDF can be equipped with a stainless steel output shaft and a nickel-plated output flange. These options increase the corrosion resistance of the gearbox. As a result, it also tolerates frequent cleaning with aggressive media, which is essential in the food and pharmaceutical industries.
A large selection of standard gearboxes from the Neugart program also allows an individually designed drive for the rotary axis of the Delta robot.
Summary
After its introduction of the NGV, the planetary gearbox for industrial forklift trucks, and the hygienic HLAE, Neugart now presents the new NDF, another gearbox solution for a special field of application. It was developed specifically for use in Delta robots and is characterized in particular by reduced inertia, very high torsional stiffness, minimal torsional backlash and high transmissible torque.
Testimonial
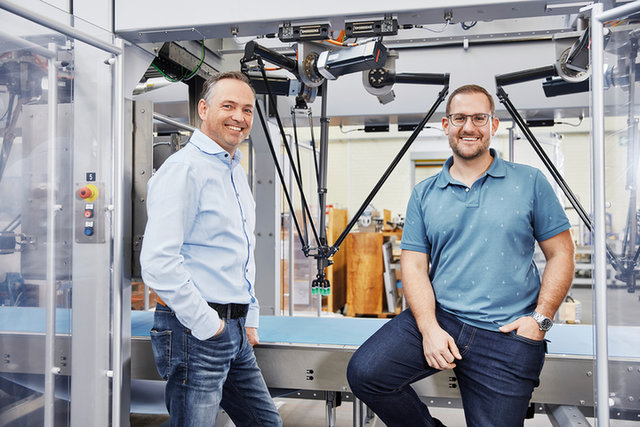
Source: Neugart GmbH
"The reliability of the gearboxes is an absolute must for us in order to meet our customers' expectations to their complete satisfaction. In our view, the NDF gearbox from Neugart offers the best overall package of performance, quality and cost efficiency. During the development of our new RPP machine platform, we worked very closely and intensely with the Neugart company and thus found the ideal gearbox solution for us."
Andreas Schildknecht and Marco Ebner | Syntegon Packaging Systems AG

Neugart is expanding its range of application-specific gearboxes with a solution specifically for Delta robots: the NDF.
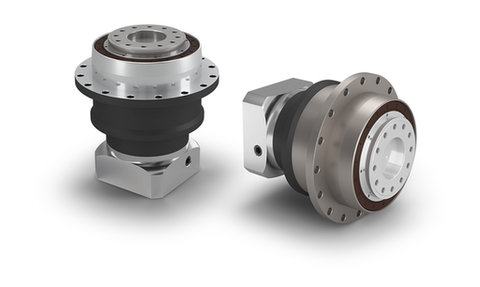
As an option, the NDF can be equipped with a stainless steel output shaft and a nickel-plated output flange.
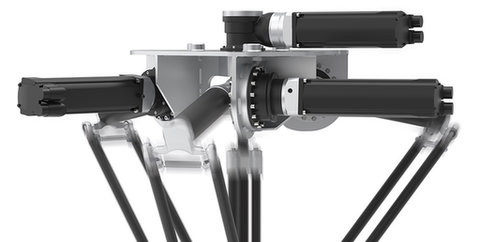
The gearbox needs to operate highly dynamically with extreme precision during constantly changing directions of rotation.
About Neugart:
Neugart GmbH is a leading global manufacturer of high-quality gearboxes and drive systems for automation equipment. Since it was founded in 1928, the company has been headquartered in Kippenheim, Germany, and is now represented worldwide by its own subsidiaries and a dense network of distributors. Neugart stands for the highest quality, reliability and innovation and has established itself as a competent partner for customers from a wide range of industries.
Neugart GmbH · Keltenstraße 16 · 77971 Kippenheim Deutschland
+49 7825 847-0 · sales@neugart.com