TECHNOLOGY
A helping hand: how is robotics improving food and beverage packing?
Robotic technologies have proved their place in helping to keep food and beverages safe. In no small part, this has been due to their ability to monitor and manage the packing stages of manufacture. Joe Baker investigates the trends that have fuelled the robot revolution and how packaging might be further automated in the future.
Image courtesy of Tetra Pak
The robots are coming. Scientists, Hollywood film directors and anyone who has watched this viral YouTube clip can attest as much. However, in the packaging world robots are already an intrinsic part of the process, and are growing smarter as businesses shift towards automation.
Complex and stringent rules surrounding food and beverage packaging may have slowed the adoption of robotics in the past, but as the cost of raw materials and pressure from retailers has escalated, robots have become an increasingly attractive method for boosting bottom lines.
Research by the Association for Packaging and Processing Technologies has shown that almost a third of food processing operations already use robotics in their facilities. Another survey carried out by the organisation revealed that 94% of food packaging operations were already using robotics last year.
The production and distribution of robots for packing purposes has become central to the activities of major companies including FANUC, ABB and Rethink Robotics. Changing packaging trends, labour shortages and a growing interest in the benefits of automation have created a packaging landscape in which robots aren’t just the future – they are the here and now.
I, packaging robot: from heavy lifting to production flexibility
Historically, robots have been used for heavy lifting tasks such as palletising and packing. However, as technology has advanced, robots have been able to take on more dexterous tasks, from picking and placing of randomly oriented foods to complex operations such as de-panning (removing baked goods from trays) and de-nesting (taking empty packages out of a stack). This means that robots can now play a role in primary, secondary and tertiary packaging.
Machines can take the mantle from humans partly due to their speed, accuracy and consistency. Popularised ‘delta’ robots (also known as parallel arm robots) have seen increasing use in factories since the 1980s, with the fastest executing up to 300 picks per minute. To give a real-world example, robotics specialist Sewtec recently created a bespoke packaging machine for Tata Global Beverages capable of packing 2,000 tea bags every minute.
However, possibly the greatest boon of robotics is flexibility – an advantage particularly important in an era when operators might need to swap out the products they are picking/packing at the flick of a switch.
A robot doesn’t need a holiday, it doesn’t need a coffee break, and it always turns up to work on time
“It really comes down to making companies more competitive by increasing the efficiency and the production flexibility,” says ABB global product manager Roy Fraser. “This is why the majority of people that buy their first robot come back and buy more.”
“A robot doesn’t need a holiday, it doesn’t need a coffee break, and it always turns up to work on time, and to be quite frank those are significant efficiencies for a company.”
In January 2018, a survey by the Association of Labour Providers found that 70% of food and beverage manufacturing companies were suffering from a shortage of low and unskilled labour. Robotics have been seen as a solution to such shortages. Although their implementation comes with the same suspicion (i.e. will I wake up to find C-3PO doing my job), some experts say that automation will lead to an increase in higher skilled jobs.
Collaborative robots: forging teamwork
Until this decade, many robots were pre-programmed, standalone contraptions kept separate from employees for health and safety reasons. Fraser says that one of the most important trends in recent years has been a move towards collaborative robots (or ‘cobots’) designed to work alongside humans.
In food and beverage packaging, cobots are increasing cost efficiencies through lower production costs and waste of raw materials, as well as being safer and easier to operate. Universal Robots, one of the companies that pioneered cobots in the late 2000s, creates machines fitted with a panel and touch screen that allows them to be programmed by employees more easily. The upshot is that robots are easier to maintain and safer to work with.
“The robot and the human can be working in very close proximity without fencing and the robot behaviour is intrinsically safe when working with a human,” says Fraser. “That reduces the complexity, it reduces the space that the robot takes up for that function in the factory, it means that people can work with robots directly, and you can actually do collaborative work with the robot.”
ABB’s main product in this area, YuMi – which Fraser says is the "world’s first truly collaborative robot" – essentially resembles two arms on a torso and is capable of carrying out precise repetitive tasks.
“So far we're really happy with the reception that YuMi has had,” says Fraser. “It only weighs 20-25 kilos – so if you want to pick it up and move it to another station tomorrow you can.”
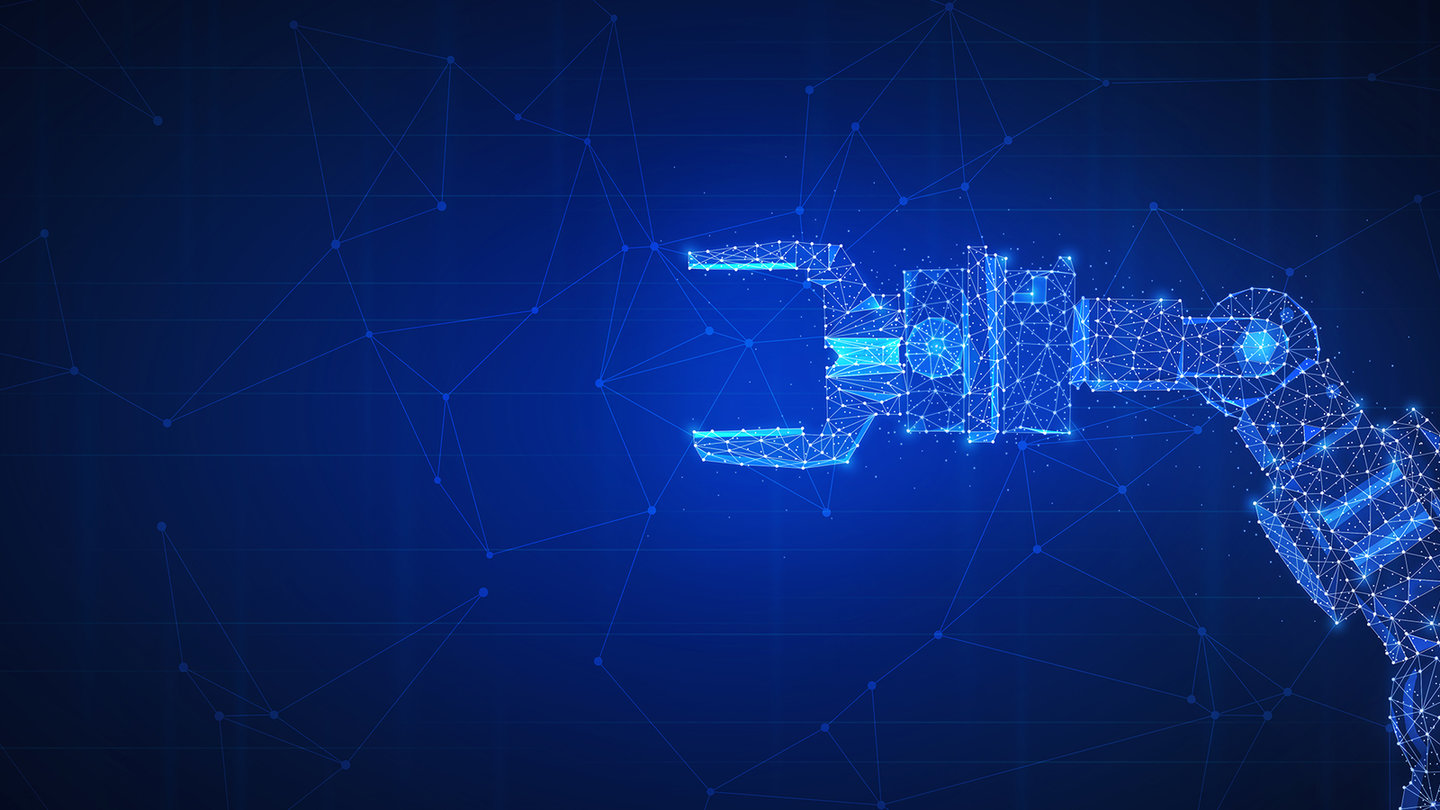
Keeping up with trends: shelf-ready packaging and product life cycles
Changes in the packaging industry have had an impact on robots. One of these is an increased focus on shelf-ready packaging – packaging that is delivered to a retailer in such a way that it is optimised for efficient stocking and brand promotion.
“That has meant that we've had to consider the flexibility of the solution,” says Fraser. “We need more than four-axis solutions to be able to do that and that’s where we've sort of looked with collaborative robots – they've been very helpful in this area.”
Robots facilitate the move from high volume low mix to low volume high mix
The packaging industry is also responding to a demand for shorter product life cycles. Fraser says that ABB has been responding to moves towards ‘high mix, low volume’ product lines, which require swifter changes to operating lines that robots can deliver.
“Now you might run for a couple of hours and then have to change your line over to run another packaging type – and then four hours later you might be changing it again,” explains Fraser.
“If you have very dedicated machines for high volume – to change it for another product can be quite difficult. But a typical six-axis robot has six degrees of freedom so it can do many more tasks in a different way, compared to harder automation which would be dedicated. Robots facilitate the move from high volume low mix to low volume high mix – this is something we are seeing across the board.”
What does the future hold? AI, big data, and the digital story
The development of artificial intelligence and big data will improve packaging in the future. As time goes on, the focus is steadily becoming about how robots are able to become increasingly interconnected, increasing efficiency.
Fraser says that one of ABB’s main focuses moving forward will be what he calls the ‘digital story’. In particular, ABB Ability is an Internet of Things-focused venture that aims to connect any electrical device to a local network, as well as a cloud-based system for data capture. Connecting robots to each other and to the cloud will enable users to track the performance of their packaging systems more effectively.
We see the industry and particularly the packaging industry evolving in the future to becoming much more digital
“If you look at our digital services today we have over 70 million digitally enabled devices,” Fraser says. “Until recently – all of these robots and machines – they were kind of like islands of automation.
“ABB Ability gives us tools and techniques to be able to join these islands of automation together and to be able to understand their actual performance related to the conditions. The technology is quite mature – we're always making improvements to our software – but providing this kind of service is where we see the next big efficiency gain.”
“We see the industry and particularly the packaging industry evolving in the future to becoming much more digital and having much more real-time information that will drive the efficiency of the factory of the future.”